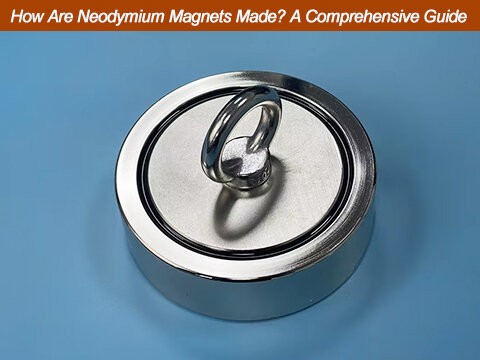
Overview of Neodymium Magnets
Neodymium magnets, also known as NdFeB magnets, are powerful permanent magnets made from an alloy of neodymium, iron, and boron.
Neodymium magnets are the strongest type of permanent magnet commercially available. Their superior strength and durability make them ideal for a wide range of applications, from everyday items to critical components in advanced technology.
Raw Materials and Initial Processing
Composition of Neodymium Magnets
Neodymium magnets are primarily composed of three elements: neodymium (Nd), iron (Fe), and boron (B), forming the alloy NdFeB. The typical composition of neodymium magnets is approximately 70-75% iron, 15-20% neodymium, and 1-2% boron, with small amounts of other elements such as dysprosium or praseodymium added to enhance specific properties.
-
Neodymium (Nd): A rare earth metal, neodymium is a crucial component that imparts strong magnetic properties to the alloy. It is extracted from minerals such as monazite and bastnäsite.
-
Iron (Fe): Iron is the primary metal in the alloy, providing the structural framework and enhancing the overall strength of the magnet.
-
Boron (B): Boron is added to the alloy to improve its magnetic properties and thermal stability.
Sourcing and Preparing Raw Materials
The first step in the production of neodymium magnets involves sourcing high-purity raw materials. Each element must be carefully extracted and refined to ensure the highest quality end product.
-
Extraction of Neodymium: Neodymium is extracted from rare earth minerals through a series of chemical processes. The ore is first crushed and ground, then subjected to a flotation process to separate the neodymium-rich concentrate. This concentrate is further refined using solvent extraction and ion exchange methods to produce high-purity neodymium oxide.
-
Reduction to Neodymium Metal: Neodymium oxide is converted to neodymium fluoride or chloride, which is then reduced using calcium or lithium to produce metallic neodymium. This metal is then cast into ingots for further processing.
-
Iron and Boron Processing: High-purity iron and boron are sourced from reputable suppliers. The iron is typically in the form of iron oxide, which is reduced to metallic iron using carbon. Boron is usually sourced as ferroboron, an alloy of iron and boron.
Alloying and Melting
Once the raw materials are prepared, they are combined in precise proportions to form the NdFeB alloy. The alloying process involves melting the raw materials together in a vacuum induction furnace.
-
Melting Process: The neodymium, iron, and boron are placed in a vacuum induction furnace and heated to a temperature of around 1,300-1,500°C (2,372-2,732°F). The vacuum environment prevents oxidation and contamination of the materials. The elements melt and mix thoroughly to form a homogeneous alloy.
-
Formation of Ingots: The molten alloy is then poured into molds to form ingots. These ingots are allowed to cool and solidify, creating the base material for the magnets. The ingots are then removed from the molds and inspected for any defects or impurities.
Strip Casting and Hydrogen Decrepitation
The solidified ingots undergo further processing to transform them into a fine powder, which is essential for creating the final magnet shape and enhancing magnetic properties.
-
Strip Casting: The ingots are remelted and cast into thin strips using a strip caster. This process rapidly cools the alloy, creating thin, brittle strips with a fine grain structure. The rapid cooling helps to improve the magnetic properties of the material.
-
Hydrogen Decrepitation: The thin strips are subjected to hydrogen decrepitation, a process that involves exposing the material to hydrogen gas. The hydrogen is absorbed by the alloy, causing it to expand and break into a fine powder. This fine powder is easier to handle and shape during the subsequent pressing and sintering processes.
Neodymium Magnets Manufacturing Process
Alloying and Melting
The manufacturing process of neodymium magnets begins with the alloying and melting of the raw materials to form the base NdFeB alloy. This step is crucial for achieving the desired magnetic properties and structural integrity.
-
Melting Process: The prepared neodymium, iron, and boron are placed in a vacuum induction furnace. The vacuum environment is essential to prevent oxidation and contamination. The furnace heats the materials to around 1,300-1,500°C (2,372-2,732°F), causing them to melt and mix thoroughly. The result is a homogeneous molten alloy with uniform composition.
-
Formation of Ingots: Once the alloy is fully melted and mixed, it is poured into molds to form ingots. These ingots are allowed to cool and solidify, creating solid blocks of the NdFeB alloy. The solidified ingots are then removed from the molds and inspected for any impurities or defects, ensuring the quality of the starting material for subsequent processes.
Powder Milling and Sintering
The fine powder produced through hydrogen decrepitation is further refined and processed to create the final magnet shape.
-
Powder Milling: The fine powder is milled to achieve the desired particle size and consistency. This step ensures that the powder particles are uniform, which is essential for producing magnets with consistent properties. The milling process may involve jet milling or ball milling, depending on the required particle size distribution.
-
Sintering Process: The milled powder is then compacted into the desired shape using a press. The compacted powder is placed in a sintering furnace and heated to a temperature just below the melting point of the alloy. This process, known as sintering, causes the powder particles to bond together, forming a solid, dense magnet with the desired shape and magnetic properties.
Aligning and Pressing
Before the sintering process, the powder particles must be aligned and pressed to achieve the desired magnetic orientation.
-
Aligning the Powder: The milled powder is placed in a magnetic field, which aligns the particles in a specific direction. This alignment is crucial for achieving the optimal magnetic properties of the final magnet. The alignment process may involve the use of external magnetic fields or pulse magnetic fields, depending on the desired magnetic orientation.
-
Pressing the Powder: After the powder particles are aligned, they are pressed into a compact shape using a high-pressure press. This pressing process ensures that the powder particles are densely packed, which is essential for achieving the desired strength and magnetic properties. The pressed compact is then ready for the sintering process.